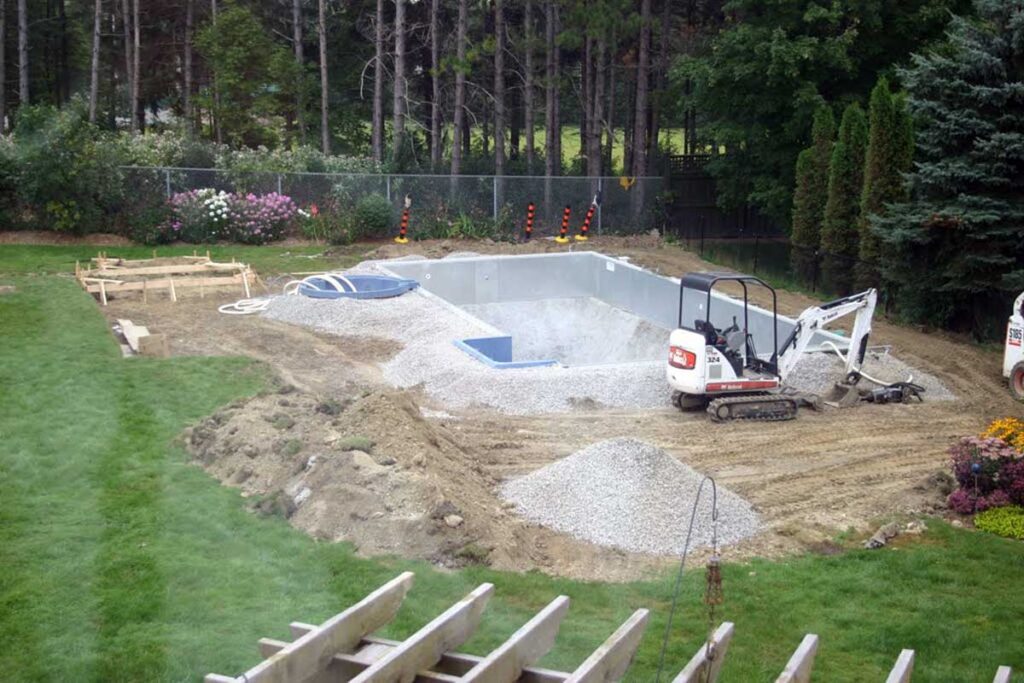
Advantages and Drawbacks of Different Swimming Pool Construction Methods
When homeowners are contemplating the installation of an inground pool, despite some agonizing over the costs of construction and ongoing maintenance, this could actually be one of the more straightforward decisions they will need to make – essentially, their options are to proceed (take the plunge?) or not to proceed.
Once they have opted to move forward with their investment in a new swimming pool, the decisions start to become more complex with respect to such matters as:
- Size, shape, and depth
- Decking and landscaping
- Equipment and accessories
- And much more
Perhaps one of the biggest and most challenging aspects will be deciding on which of the following construction methods is preferred, as it will be quite difficult, not to mention rather expensive, to have a change of heart after-the-fact:
- Vinyl
- Concrete
- Fiberglass
As is often the case with other construction methods where there are multiple options available, each type of swimming pool material will have its associated pros and cons. The considerations provided below are for comparative purposes only:
- Vinyl pool
- Less-labour intensive and the least expensive option – installed in ~3 weeks
- Pre-fabricated – obtainable in almost any customized shape and depth
- Has a vinyl liner – available in many different colours and design patterns
- Liner material is a smooth and non-porous surface – deters growth of algae
- Will likely need to replace the liner over the life of the pool – can be costly
- Colour/pattern of liner will fade over time as a result of regular chlorine use
- Liner is not very thick – susceptible to damage from debris, toys, carelessness
- May be a deterrent to home resale value due to inevitable liner replacement
- Concrete construction (also known as gunite)
- Offers the greatest amount of options in terms of pool size, shape, and depth
- Also provides more flexibility with respect to customized features and designs
- Durable material – is able to withstand weather extremes in the Toronto area
- Customized designs and features lend a high aesthetic appeal to the property
- Will require re-surfacing and re-tiling over its lifecycle – at a rather high cost
- Concrete is porous – more chemicals/filtration are needed to prevent algae
- More maintenance than other methods, especially brushing walls and bottom
- The lengthiest installation time of all swimming pool construction methods
- Fiberglass
- Offers the fastest installation of all swimming pool construction methods
- Single pre-formed, pre-finished units in a variety of shapes, colours, textures
- Seats and steps can also be incorporated directly into a fiberglass shell
- Resurfacing is not required and there is no vinyl liner that may need replacing
- Less maintenance/chemicals – smooth surface inhibits algae adherence/growth
- Lower maintenance costs/longevity of fiberglass can be advantages in re-sales
- Higher initial purchase price can be prohibitive for some homeowners
- Less customizable than other swimming pool construction methods
- Tends to be rather restrictive in terms of pool shape, depth, and width
- Although repairs are infrequent, colour finishes are difficult to match
While there will be some variability in the installation steps for each of these swimming pool construction methods, there is also a high degree of consistency across these methods regardless of the pool size, shape, or type of material selected. From a general perspective, pool construction customarily entails the following:
- Preparation
- Site survey, location of underground utilities, acquiring a permit
- Ensuring a clear route of entry and exit for crew and equipment
- Design
- Size and positioning of the swimming pool within the backyard
- Orientation of the pool with respect to plumbing and hydro needs
- Excavation
- In accordance with by-laws and the preparations and design specs
- Installation
- Fiberglass – one-piece shell is basically inserted into the excavated area
- Concrete – solid panels are erected along the sides of the excavation then the interior is shaped/formed and lined with concrete
- Vinyl – also requires solid panels along the sides – the bottom is either poured concrete or sand and the sides are often padded before being covered with the liner (usually a single pre-cut piece)
- All three construction methods need some form of external reinforcement or stabilizing – either poured concrete or gravel
- Features and accessories
- Proper fencing (if not pre-existing) and a pool deck or patio are basic needs
- The last items to be installed are often any non-essential but desired elements such as heaters, water features, slide and/or diving board, outdoor lights, etc.
It should be readily apparent that installing an inground swimming pool, independent of the different construction methods, is a rather extensive process in terms of the time, precision, and the diverse skills and equipment required. Although homeowners may be inclined to attempt this process on the own as a means of saving some of the costs, it is highly advisable to defer such efforts to the expertise of a professional pool contractor such as Jones Pools.
Click here for information on the swimming pool construction methods employed by Jones Pools.
If you interested in installing an inground swimming pool this spring or summer, call the pool construction professionals from Jones Pools today at 905-642-9522 or 905-862-0414 to discuss the various design options and construction methods that best suit your property and your lifestyle.